It was a brisk morning as the final checks on the lakebed and in the control room were nearly complete for the X-56A to take flight at NASA’s Armstrong Flight Research Center in California.
The flight crew worked with the ground crew to check that the control surfaces on the remotely piloted aircraft were responsive to commands. The center’s Dryden Aeronautical Test Range, the range safety officer and the Edwards Air Force Base tower were added in the communication loop and ready.
Test conductor Jake Schaefer directed the team as a symphony conductor manages a performance. He is also the dedicated flight crew communicator and a test information filter to help the pilots manage their work load.
Schaefer checked for final confirmation that the aircraft was ready for flight. “Controls,” he called out. “Go” was the response. Similarly, representatives from the launch team on the lakebed, structures, systems and Cheng Moua, the X-56A project manager, signaled that the vehicle was ready to fly.
Reports from a weather balloon and from a T-34 aircraft circling overhead were evaluated as the final checks were completed. The X-56A aircraft moved down the runway faster and faster until the wheels no longer touched the ground and co-pilot Dana Purifoy called, “NASA five-six is airborne.”
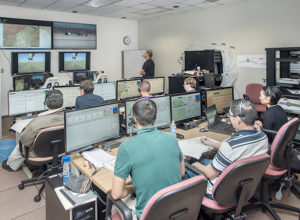
As the aircraft approached a test point, the flight was monitored by experts in different disciplines, who were seated in rows behind the pilots. The experts reviewed information displayed on the screens in front of them. “Mark” was called out to begin a test point. When the needed data had been collected from a maneuver, “complete” was called. If more data were needed, “repeat” was called.
During the flight, the X-56A suppressed a potentially destructive vibration called flutter, which permitted research of the aircraft’s lightweight, flexible wings. The results of the research could enable future airliners to use similar wing designs to conserve fuel. The X-56A team is also facilitating the development of tools and technologies and acquiring data to validate modeling techniques.
It’s not just the aircraft readiness that determines if the mission will fly. Weather, turbulence at test altitudes, lakebed conditions, pilot availability, and experiment or aircraft challenges can make or break flight plans.
“They are not just going out to fly, they are doing experiments,” Moua explained. “The conditions have to be right to successfully conduct the mission.”
The team understands that flight research is complicated, so they focus on what they can do. Cross training team members and selecting backups where possible enable the team to be ready when something inevitably happens.
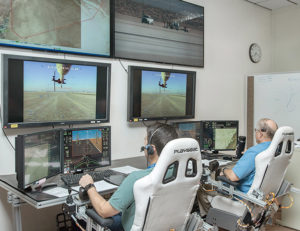
For example, before former test conductor Chris Miller transitioned to a detail assignment, he helped Schaefer, who was the controls lead, train for the certification required for that role. Matt Boucher then became the new controls lead. It’s a busy control room with as many as 10 people during a flight – if one is out, the show must still go on. Jason Lechniak, who is capable of monitoring data for controls, structures or systems, is an example of how the team can manage an absence.
It is stressful before takeoff to make sure the aircraft is ready and when a new test condition is reached, Miller explained.
“The way X-56A is structured, we can practice everything, which allows us to know what the test point is supposed to look like and what it feels like,” he said. “It gets stressful when things do not go as planned and that’s why we rehearse.”
Schaefer was surprised at how he felt during his first experiences as the mission controller on a different flight.
“Being mission controller felt far less stressful than the flights where I was a discipline engineer in the control room,” he said. “As an engineer, there is a large amount of data you are constantly looking at, trying to pick out anything that looks different from what was expected based on simulations or past flights. You want to spot a problem before it gets bad and pass that information to the pilots.”
The control room is similar to many others, except the pilots are seated in gaming chairs in the front of the control room – they are not flying the aircraft across the sky from its cockpit.
“Initially I thought it would be a distraction, having so many people behind me, but I realized everyone behind me is extremely focused on monitoring their particular vehicle parameters during the flight,” said chief X-56A pilot Scott “Jelly” Howe. “They are ready in an instant to call out an abort or a flutter warning call that the crew will instinctively react to thanks to repeated test rehearsals.”
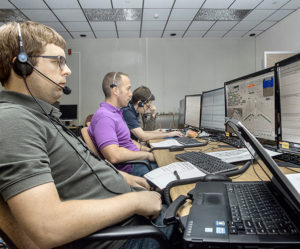
Practice adds familiarity and confidence
“Full team control room rehearsals remove any notion of distraction or being ‘watched’ and replaces that with the confidence that the folks behind me are keeping the aircraft safe,” Howe said. “That is especially important when the test points are near uncharted, higher speeds for the aircraft that may be hazardous. I’m a huge proponent of thorough, realistic test rehearsals before every flight.”
The X-56A pilots don’t have some of the physical cues of flying in an airborne cockpit, but they do have video from Armstrong videographers and a camera on the nose of the aircraft, plus cockpit displays and maps.
X-56A flights last about 30 minutes, depending on how fast the aircraft is flying. At the end of the flight, the aircraft is piloted to lower altitudes until it lands and taxis to the ground crew, who will make sure the parking brake is set, the engines are shut down and the aircraft is powered down. The X-56A is then secured to a trailer for transport back to its hangar.
The good, the bad and the unexpected from each flight are discussed in a debrief about an hour after each flight. Following the debrief, it is determined whether there will be a practice for the next flight later in the day. If the data and the weather are good, the team might be able to come in the next day and do it all again. Regardless of the situation, it’s certain the team will be ready.