They call it the “tanning bed.”
The array of quartz lamps, built to simulate the thermal stress of hypersonic flight, can crank out temperatures in excess of 2500 degrees Fahrenheit. Raytheon Missiles & Defense, a Raytheon Technologies business, uses it in tandem with digital engineering methods such as modeling and simulation, as well as wind-tunnel testing, to evaluate and improve the performance of hypersonic airframes — those that fly faster than Mach 5 — without time and expense of actually taking them to a physical test range.
“You can park a missile in it or a section of a missile,” said Adam Wood, an engineering fellow.
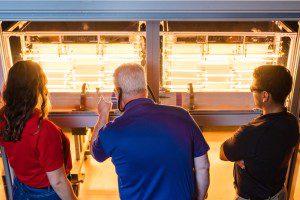
Heat is one of the key problems engineers have to overcome in designing hypersonic airframes.
When missiles travel that fast, they push large volumes of air out of the way. That creates friction — so much heat, in fact, that it would cause many common materials such as aluminum to disintegrate, said Ralph Klestadt, a chief engineer for hypersonics.
Apart from that, Klestadt said, even if an airframe stays intact, the heat can distort its shape and affect its maneuverability.
“As a system starts to heat up, parts of it will be really hot while others aren’t quite yet, causing pieces of the vehicle to grow at different rates,” Wood said. “The shape begins to change and that affects how it flies through the air. It becomes a structural issue.”
There are a number of ways to overcome the heat problem — design elements, novel materials, special coatings, and so on — but no matter the method, engineers have to make sure it’s going to work. That’s where the “tanning bed” comes in.
Flexible framework