FORT IRWIN, Calif. — Fort Irwin seems to be a quieter place these days. The constant back and forth of Rotational Training Units has ceased, units operate at minimal manning and large gatherings are replaced by teleconferences.
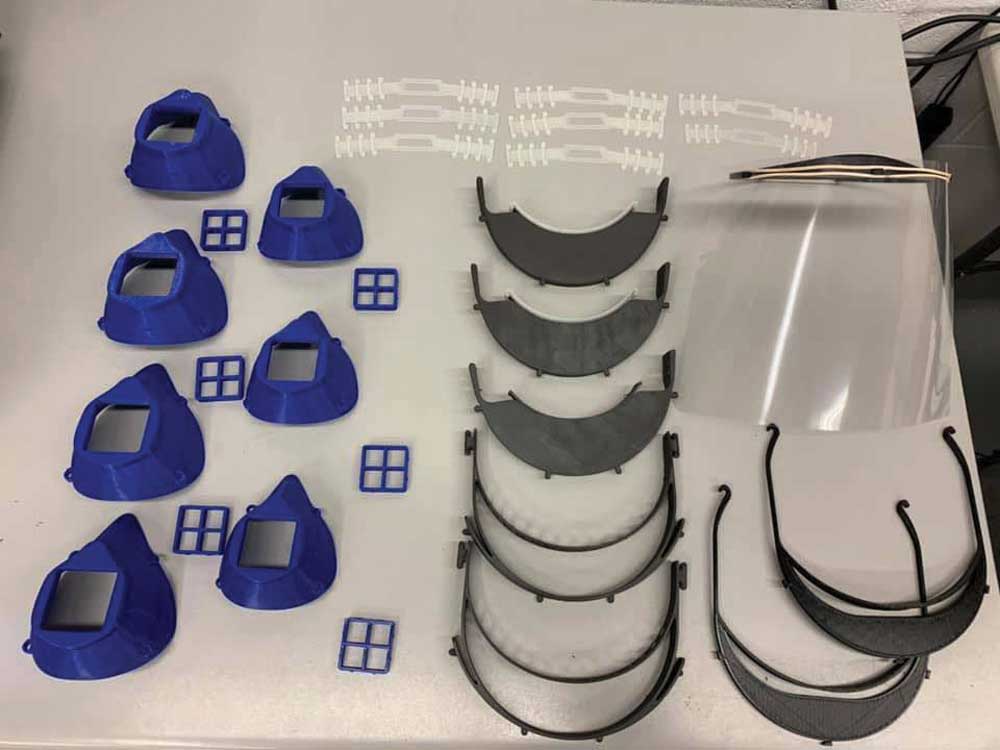
The 11th Armored Cavalry Regiment is adjusting to this ‘new normal,’ alongside the rest of the National Training Center and the nation as a whole, doing their part to flatten the curve. In this quiet time, one group of the 11th Armored Cavalry Regiment’s “essential workers,” the Service and Recovery Section (S&R) of Maintenance Troop, Regimental Support Squadron, have stepped to the forefront of the fight against COVID-19.
S&R regularly fabricates unique and otherwise hard to come-by repair parts to support the Regiment’s rotational mission, often via 3-D printing, in a process known as additive manufacturing. To maximize their efficiency with this relatively technology, S&R’s Officer in Charge, Chief Warrant Officer 2 Justin Allen, regularly correspondents with other professional 3-D printing organizations. Virtually all of these organizations have recently focused on the production of medical Personal Protective Equipment (PPE) to counter widespread shortages. Seeing the situation at hand, Allen was determined to do his part to slow the virus.
He used the National Institute of Health (NIH)’s online database on 3-D, printable PPE to identify both face-shields and a potential replacement for the N-95 mask. S&R’s efforts to produce the latter have focused on the ‘Montana Mask’ originally designed for the Billings Medical Clinic in Montana. The Montana Mask is specifically designed to stretch medical resources further, using one fourth of the material from a disposable surgical mask as the filter. As a result, each disposable surgical mask’s material can be used up to four times, greatly increasing stocks of PPE.
With designs for both provided by NIH and the Billings Medical Clinic’s website, makethemask.com, Allen took the initiative to conduct proof of concept production runs of both designs. These successful production runs demonstrated that S&R is able to produce a batch of four masks every eight hours with a material cost of less than five dollars per mask. The Montana Mask, while still pending clinical trials by Northern Occupational Safety and Health Association and the Food and Drug Administration for use in medical settings as a replacement for the N95, has been adopted by a number of hospitals facing PPE shortages across the nation. In addition, use of the Montana Mask falls in line with the most recent Centers for Disease and Control guidance to wear any form of mask available when unable to maintain social distance.
S&R has shared news of its successful proof of concept production with the rest of the Regiment and the U.S. Army Medical Department Activity in Fort Irwin (MEDDAC) and offered to produce supplementary PPE. While MEDAAC currently has enough PPE on hand to meet its patient demands, other opportunities for the use of S&R-produced face shields and masks exist. As of Apr. 6, S&R has already received requests to produce 68 face shields to support the DFAC and Gate Guard missions. Regardless of the mission, S&R stands ready to support.