Until recently, Northrop Grumman’s facility at Air Force Plant 42 in Palmdale, Calif., was perhaps best known as being the site where the B-2 Spirit bomber was built and assembled.
In fact, in 2019, the company and the U.S. Air Force marked the 30th anniversary of the first flight of the stealth bomber when it flew from the Palmdale facility to Edwards Air Force Base on July 17, 1989. To mark the anniversary, Northrop Grumman hosted an event at Plant 42 on Aug. 20.
While B-2 production ended some years ago, and depot maintenance is now performed in Oklahoma, work has continued at the facility in various capacities.
Northrop Grumman produces the center fuselage for the Lockheed Martin F-35 Lightning II at its ‘Palmdale Aircraft Integration Center of Excellence.’ In February 2019, Northrop Grumman announced it had delivered the 500th center fuselage for the F-35 ahead of schedule.
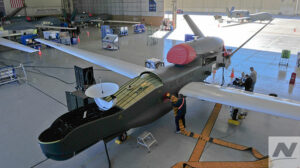
“We deliver an F-35 center fuselage every 36 hours and I am very proud to say we have made all our deliveries since the inception of the program,” said Frank Carus, vice president and F-35 program manager, Northrop Grumman. “Our dedicated team works closely with the customer and suppliers to improve quality and affordability in support of the warfighter.”
The center fuselage is designed and produced on Northrop Grumman’s integrated assembly line, a state-of-the-art facility supported by technologies exclusive to or pioneered by Northrop Grumman bringing together robotics, autonomous systems, virtual 3D and predictive automation to the forefront of center fuselage production. The facility has been recognized by various industry organizations as well.
In March 2019, the company was recognized by the National Association of Manufacturers with Manufacturing Leadership Awards for three of its aircraft manufacturing capabilities. The cutting-edge capabilities harness metadata, analytics, and virtual and augmented reality in multiple Northrop Grumman manufacturing programs.
“We have a rich history of manufacturing the most advanced products in the world,” said Kevin Mitchell, sector vice president, global operations, Northrop Grumman Aerospace Systems. “Today, we use a variety of manufacturing techniques to develop the capabilities to support our customer’s toughest missions. We are honored to be recognized for our leadership in manufacturing.”
The company was recognized for the following technologies:
• The assembly metadata integration project extracts quality data from automated systems on Northrop Grumman’s F-35 Integrated Assembly Line. It uses advanced analytics to mine data and automate an otherwise tedious manual effort for identifying discrepancies, generating reports, evaluating and documenting the quality data, and defining and directing corrective action.
• The analytics-enabled complex assemblies capability leverages analytics to assemble complex airplane parts of diverse material types. It enables Northrop Grumman to machine complex parts on divergent machines and then drill precision hole-bores. This project reduces complexity, cost, facility requirements and risk while improving throughput and design change sensitivity. Northrop Grumman uses this capability on both its manned and autonomous aircraft systems, including the High Altitude Long Endurance family of systems that comprise programs like the U.S. Navy’s MQ-4C Triton and U.S. Air Force’s RQ-4 Global Hawk.
• Northrop Grumman leverages augmented reality, virtual reality and 3D analytics to improve airframe manufacturing processes. This enables the company to capture and analyze data to gain meaningful insights into manufacturing challenges experienced by human tasks. By combining airframe manufacturing data with artificial intelligence/machine learning, AR and VR, Northrop Grumman captures human variability and work content that reduces rework, disruption and downtime. Similar to the ACA capability, this can be used across the spectrum of Northrop Grumman aircraft programs.
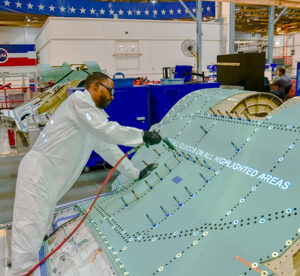
Also in March, Quality Magazine named the Palmdale facility as Quality Plant of the Year. Each year, the publication awards this recognition to a manufacturing plant in the United States.
According to Quality Magazine, the award recognizes a manufacturing facility that uses world-class technology, equipment, services and techniques to reduce scrap, rework, warranty or manufacturing costs; improve productivity or cycle time; increase capacity; or improve adherence to quality standards.
“Quality is engrained in our team,” said Cory Carruth, vice president and Palmdale site manager, Northrop Grumman. “It is part of our culture and something our employees take very personal as it’s critical to the safety of our warfighters.”
Another milestone event was the non-stop, transatlantic ferry flight of the first of five NATO Alliance Ground Surveillance aircraft. The aircraft took off from Palmdale on Nov. 20, and landed in Sigonella, Italy, 22 hours later on Nov. 21.
The NATO AGS RQ-4D aircraft is based on the U.S. Air Force wide area surveillance Global Hawk. It has been uniquely adapted to NATO requirements and will provide NATO state-of-the-art intelligence, surveillance and reconnaissance capability. This includes protecting ground troops, civilian populations and international borders in peacetime, times of conflict and for humanitarian missions during natural disasters.
But perhaps the biggest buzz surrounding Northrop Grumman at Plant 42 these days is the B-21 Raider.
In October 2015, the U.S. Air Force awarded a development contract to Northrop Grumman for the proposed bomber. In 2016, it was designated the B-21, and in October 2016, the Air Force announced it would be known as the “Raider” in honor of the Doolittle Raiders.
Press reports state that Northrop Grumman has been hiring across the board as production of the initial aircraft continues. The Air Force is expecting to purchase about 100 B-21s.
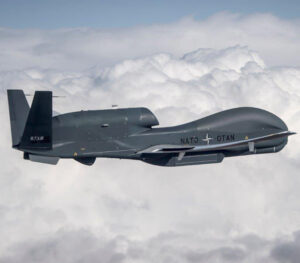
On Feb. 3, 2020, Vice Chief of Staff of the Air Force Gen. Stephen Wilson visited the B-21 Raider manufacturing facility.
During his visit to the Palmdale facility, Wilson received a tour of the production line where the build of the initial test aircraft is currently underway and a briefing on the status of the overall program. Wilson also had the opportunity to meet with the workforce and praise their continued support and commitment to building the next-generation stealth bomber.
“The innovation demonstrated by this production line is as impressive as is the partnership between industry and government,” Wilson said during the tour, which also highlighted the contributions of Northrop Grumman’s partners to the initial test aircraft. “It truly is a nationwide effort to make this bomber a reality here in Palmdale.”
The B-21 Tier 1 suppliers were announced in March 2016 and include BAE Systems, headquartered in Nashua, N.H.; GKN Aerospace in St. Louis; Janicki Industries in Sedro-Woolley, Wash.; Collins Aerospace in Cedar Rapids, Iowa; and Spirit AeroSystems in Wichita, Kansas.
No date has been set for the B-21’s first flight, but then-acting Secretary of the Air Force Matthew Donovan told the Air Force Association Conference on Sept.16, 2019, that “The first flight of the Raider will take it from Palmdale to Edwards AFB, where the legacy of excellence will continue with the reactivation of the 420th Flight Test Squadron.”
The Palmdale to Edwards flight is reminiscent of its predecessor, the B-2 Spirit. The Air Force has said flight testing will be conducted at Edwards, and on Oct. 4, 2019, the 420th FTS was reactivated; its mission — the planning, testing, analyzing and reporting on all flight and ground testing for the B-21 Raider.